LEAN: SEITON (ORDINARE)
LEAN: SEITON (ORDINARE)
Introduzione
Nell’articolo di oggi continueremo a parlare dell’applicazione della tecnica 5s. Nello scorso capitolo abbiamo parlato in linea generale della tecnica e approfondito la prima S (se non l’hai ancora letto clicca il link e recupera subito il terreno 😊).
Quest’oggi andremo a definire ed approfondire la seconda S à Seiton(Ordinare).
Il secondo step infatti ha come obiettivo quello di definire una posizione per i componenti identificati, in modo da facilitarne l’attività di utilizzo; quindi si tratta semplicemente di prendere in considerazione solo i componenti (attrezzature, strumenti, materiali, ecc..) che sono rimasti in “gioco” dalla scrematura effettuata durante l’applicazione della prima S. Infatti, tutto ciò che è rimasto nell’Area Rossa durante l’applicazione del primo step è da definirsi Inutile e quindi da eliminare dal reparto; ora non resta che trovare una posizione ideale per tutti i componenti che sono realmente utili all’esecuzione dell’attività.
In parole povere, trova il posto GIUSTO per tutto ciò che è NECESSARIO nella postazione di lavoro:
“UN POSTO PER OGNI COSA E OGNI COSA AL SUO POSTO”
In pratica i passaggi da eseguire sono i seguenti:
- Effettua delle riprese video della lavorazione, in modo da analizzare dettagliatamente la sequenza e la locazione di ogni singola operazione.
- Associa ad ogni operazione analizzata al punto precedente i componenti (attrezzature, strumenti, ecc) necessari.
- Posiziona i componenti nella loro sequenza di utilizzo e vai alla ricerca della minimizzazione degli spostamenti dell’operatore (avvicina le attrezzature e se necessario duplicale: ti accorgerai come il costo sostenuto nell’acquisto delle attrezzature doppie verrà recuperato in un batter d’occhio con il miglioramento dell’efficienza produttiva).
- Metti più vicini i componenti con maggior frequenza di utilizzo in modo da minimizzare gli sprechi.
- Mantieni gli strumenti a VISTA: non nascondere le attrezzature, disponi sempre tutto a “portata” di occhio.
Questi sono solo alcuni dei passaggi che devono essere messi in pratica per ottenere l’obiettivo principale della seconda S: “In qualsiasi momento ci deve essere ordine”.
I benefici che riscontrerai nell’applicazione del secondo step della tecnica saranno molteplici e l’efficienza produttiva della singola lavorazione aumenterà di conseguenza: pensa a quanto tempo viene perso all’interno di ogni azienda nella ricerca di attrezzature e strumenti. Adesso invece l’operatore conosce già la posizione dell’attrezzatura e si concentrerà solo ed esclusivamente sull’esecuzione dell’attività di lavorazione.
Di seguito ho riportato due esempi di postazioni in ordine (nella prima foto lo scaffale della linea di assemblaggio con attrezzature e componenti, nella seconda foto il pannello delle attrezzature per la saldatura delle casse):
Figura 1 Scaffalatura Linea di Montaggio Figura 2 Pannello attrezzatura saldatura Cassa
Come conclusione all’articolo, vorrei ripetere nuovamente l’importanza del confronto e del coinvolgimento degli addetti nella fase di riordino dei componenti. Farsi consigliare la disposizione dei componenti da chi passa la stragrande maggioranza della sua giornata nel reparto è una strategia sicuramente ottima per ottenere risultati sicuramente maggiori delle aspettative #(di nuovo)COINVOLGIMENTODITUTTI 😊.
Concludo dandoti appuntamento al prossimo articolo in cui parleremo della 3°S à Pulire (“Seiso”).
Alla prossima,
A presto,
Paoletti Leonardo
Lean Manager Officine Cucini Srl.
Lean Day 07/07/2020
BARBERINO VAL D’ELSA – mart. 7/7/2020
Martedì 7 luglio 2020 abbiamo ospitato presso la nostra sede il #LeanDay2020, giornata in cui si riuniscono i responsabili di varie aziende che hanno sviluppato interesse verso il modello Lean e si fa visita nelle aziende che lo hanno già applicato.
Officine Cucini ha iniziato a lavorare con il metodo Lean nel 2014.
Grazie a questa scelta, siamo riusciti a raddoppiare la nostra capacità produttiva e abbiamo messo al centro dell’azienda le persone: i dipendenti, i collaboratori e i nostri clienti.
Grazie a tutti i partecipanti e ad Alessandro Parisi della CTQ spa.
Lean - le 5S - la prima S: SEIRI
LEAN - LE 5S
LA PRIMA S: ➞ SEIRI
Introduzione
5S è una semplice tecnica che crea le condizioni per la stabilità dei processi e per l’attività di miglioramento continuo all’interno dell’azienda.
La tecnica si fonda su dei principi di facile applicazione e tuttavia non mantenuta nel tempo dalla stragrande maggioranza delle aziende (VIENE DATA MOLTO PER SCONTATA ☹); infatti, più che una metodologia fine a se stessa, come vedremo più avanti nelle prossime settimane, la tecnica 5S deve diventare una filosofia di pensiero e un modo di comportarsi (di fare le cose) che accomuna tutti i singoli individui che fanno parte dell’organizzazione.
La tecnica, come intuibile dal nome, è divisa in 5 semplici passaggi la cui nomenclatura deriva dal giapponese. Nell’ordine, la tecnica si divide in:
- Separare(“Seiri”): separare ciò che è necessario da ciò che è inutile
- Ordinare (“Seiton”): definire una posizione per i componenti identificati, in modo da facilitarne l’attività di utilizzo
- Pulire (“Seiso”): rimuovere ed eliminare le fonti di sporcizia nell’area di lavoro
- Standardizzare (“Seiketsu”): stabilizzare le prime tre fasi con un metodo standard
- Sostenere (“Shitsuke”): applicare continuativamente la metodologia
Oggi parleremo della prima delle 5S: Separare.
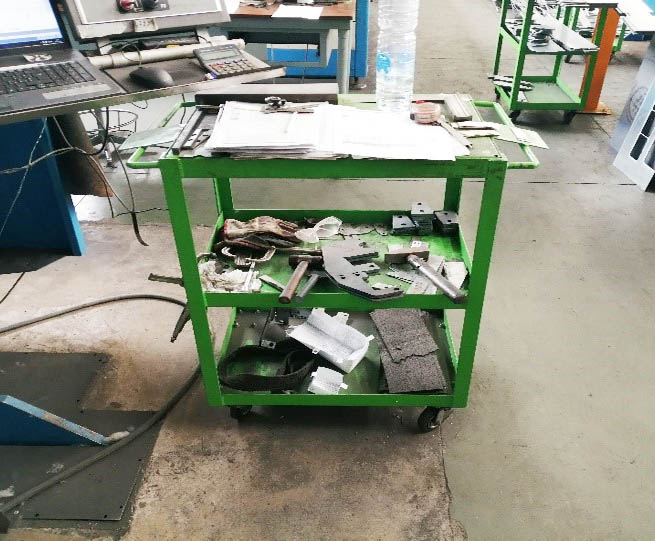
Ah, fai delle foto della situazione di partenza della tua postazione e conservale, ci torneranno utili alla fine di questo viaggio 😊.
L’esempio che ci seguirà fino alla fine di questa serie è l’applicazione delle 5s sul carrello del nostro reparto di Piega (ecco, nella Figura 1, la foto della situazione di partenza ☹).
Ma torniamo a noi, eravamo rimasti alla prima delle 5S ➞ Separare
- Stabilire i confini (la zona, il reparto, il macchinario, la postazione di lavoro, ecc..) a cui applicare la tecnica.
- Delimitare un’area ristretta definita AREA ROSSA (traccia una zona rettangolare sul pavimento con un nastro rosso e bianco, dev’essere una cosa semplice ma visibile)
- Spostare TUTTO ciò che si può spostare all’interno dell’Area rossa (Fig.2)
- Si riinizia a lavorare prendendo solo ciò che è necessario dall’AREA ROSSA per un periodo di tempo prestabilito (scegliere una settimana, due settimane o un mese ad esempio come intervallo di tempo in base alla frequenza di ripetizione del processo).
A questo punto, rimarranno solo le attrezzature e i componenti che realmente sono necessari: tutto il resto deve essere allontanato definitivamente. Vi renderete conto di quanto spazio era occupato da attrezzature e materiali INUTILI. Quindi, tutto ciò che è rimasto all’interno dell’Area Rossa alla fine del periodo prestabilito è da considerarsi inutile e da eliminare.
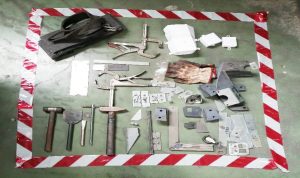
Il luogo di lavoro NON deve servire da contenitore, tutto ciò che è inutile è muda (spreco)!!!
Ah, quasi dimenticavo, nell’applicazione della tecnica, il principio fondamentale è il NON pensare di poter decidere tutto dai piani alti dell’azienda; è necessaria l’approvazione e il coinvolgimento delle persone che quotidianamente hanno a che fare con la postazione di lavoro. Tutti e dico tutti devono essere coscienti dell’obiettivo e della finalità della tecnica. Lo strumento migliorerà l’attività dell’azienda in senso completo, a partire dalla qualità del lavoro delle persone. #COINVOLGIMENTODITUTTI
Non perdetevi il prossimo appuntamento in cui parleremo della seconda S ➞ ORDINARE(“SEITON”).
A presto,
Paoletti Leonardo
Lean Manager Officine Cucini Srl.
Comunicazione per i nostri clienti
COMUNICATO PER I NOSTRI CLIENTI DURANTE LA FASE DI EMERGENZA COVID-19
Gentili Clienti,
data la complicata situazione che il nostro intero paese sta affrontando a causa della rapida diffusione del Covid-19, giovedì scorso abbiamo deciso di chiudere le nostre attività per tutelare la salute dei nostri collaboratori e dei nostri fornitori. Ciononostante crediamo che ogni crisi nasconda in sé anche delle opportunità di crescita e di miglioramento per permetterci, e ci auguriamo tutti il prima possibile, di ripartire con entusiasmo e con maggior consapevolezza su ciò che può essere aggiornato per offrire un servizio sempre più efficiente per voi, per i nostri fornitori e per i nostri collaboratori interni ed esterni.
Come probabilmente già saprete, l’ultima recente crisi, quella del 2008 ci fu di grande stimolo per riorganizzare tutta la produzione industriale in termini di Lean Production. Questo stravolgimento dal punto di vista di organizzazione interna ci permette oggi di essere immediati nella gestione delle vostre richieste, siano esse standardizzate o personalizzate.
Vi assicuriamo quindi che non appena questa fase emergenziale si sarà conclusa, saremo in grado di accogliervi con la stessa professionalità e passione che contraddistingue la nostra azienda, addirittura con ulteriori miglioramenti, sul fronte commerciale, comunicativo ed alcuni perfezionamenti di prodotto.
Per ovvi motivi, adesso non ci è possibile essere presenti nei vostri confronti personalmente, per questo stiamo potenziando i nostri canali online, dalla maggiore interattività del nostro sito ufficiale cucini.it, ai nostri canali social come Facebook, Youtube e Linkedin, che vi invitiamo a seguire per poter così interagire ed accorciare le obbligate distanze.
Riteniamo che essere in contatto, sia in termini professionali che in quelli personali, sia di fondamentale importanza in questo momento in cui siamo costretti per il bene della collettività al distanziamento. Per questo ci teniamo a darvi conferma della nostra vicinanza.
Siamo come sempre a vostra disposizione,
A presto,
Simona Cucini.
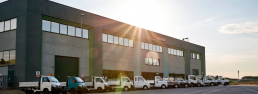
Openday Cucini School 15/11/2019
BARBERINO VAL D’ELSA – ven. 15/11/2019
Venerdì 15 novembre 2019, si è tenuto il primo Openday organizzato da Cucini School dove gli studenti della 4° e 5°A Meccanica dell’Istituto Tecnico Industriale Sarrocchi di Poggibonsi sono stati ospiti presso il nostro stabilimento di produzione.
L’incontro, della durata di 5 ore, è vertito sul mondo del lavoro ed è stato studiato per fornire ai ragazzi informazioni pratiche e strumenti che saranno loro indispensabili una volta usciti da scuola. Un occasione preziosa anche per vedere dall’interno come si svolge una giornata lavorativa in uno stabilimento industriale e per parlare con i collaboratori interni ed esterni, gli ingegneri, gli operai specializzati, i consulenti e i dirigenti.
La mattinata si è svolta così:
- Introduzione della titolare Simona Cucini: chi siamo e come è nata la nostra azienda
- I fornitori: Officina Protani
- I consulenti: il Dott. Alessandro Parisi della CTQ Spa ha spiegato perchè Officine Cucini ha applicato il metodo di produzione basato su Lean Manufacturing. Cosa è cambiato da prima ad ora.
- Giro in azienda: i ragazzi hanno visitato lo stabilimento, i reparti, gli uffici, la verniciatura, il montaggio
- I fornitori: OpenjobMetis di Certaldo. Valentina Mannari e Maggie Rampani hanno spiegato come funziona il lavoro di una agenzia interinale. Hanno fornito preziosi consigli su come scrivere il proprio curriculum vitae e su come presentarsi al primo colloquio.
- I consulenti: Davide Bini e Alessandro Goti di Genio in 21 Giorni ci hanno dato una dimostrazione pratica di come sia possibile immagazzinare una quantità di dati impressionante e studiare in modo più veloce ed efficiente con il loro metodo
Ringraziamo gli insegnanti e i ragazzi di essere venuti. Ci auguriamo di aver centrato il nostro obiettivo organizzando una giornata utile per loro.